Have you ever wondered about the creation process behind the metal objects we see everywhere—from handrails to car parts? The answer lies in a specialized craft known as metal fabrication. This intricate and specialized process involves shaping raw metal materials into tailored products or components using advanced equipment and expert skills.
Metal fabrication plays a pivotal role in our modern society, catering to construction, automotive, aerospace, and various other industries. Its significance extends beyond manufacturing; it's the catalyst that brings unique concepts to fruition, transforming raw materials into innovative, functional products that drive progress.
Join us as we unravel the journey from concept to custom metal fabrication, exploring the intricate steps that convert ideas into tangible metal wonders.
Diverse Applications of Metal Fabrication: From Structural Foundations to Commercial Essentials
Metal fabrication is defined by its versatility, encompassing an extensive array of applications across numerous diverse markets. From foundational structures like stairs, walkways, and platforms to the intricate components such as nuts, bolts, and screws that fortify them, metal fabrication is everywhere.
Commercial sectors rely significantly on metal fabrication for essentials like handrails, awnings, and conveyors. As a rule of thumb, if it's a metal entity, chances are it has undergone the process of fabrication at some stage.
From Idea to Blueprint: Nurturing Concepts into Precise Metal Fabrications
At Shupe Fabrication, our primary role is to transform client ideas or concepts into tangible, high-quality, and durable metal fabrications. This transformative journey starts with skillfull and meticulous conceptualization and design.
Whether it's a groundbreaking idea bound for commercialization or a bespoke requirement demanding specialized tools, each metal fabrication project requires gaining a comprehensive understanding of the client's needs. Leveraging our expertise and honed skills, we navigate the specialized path towards actualizing this vision.
After that point, we assess project feasibility, offer recommendations for enhancements, and refine the concept for an optimized final product. Guided by our expertise, the client's initial concept flourishes into a well-defined design, serving as the cornerstone for the forthcoming metal fabrication process.
Exploring Methods of Metal Fabrication
Metal fabrication encompasses a spectrum of methodologies tailored to diverse project needs. When most people hear "metal fabrication", welding is likely the first thing that comes to mind. However, there are several pivotal techniques integral to the process.
Cutting
Cutting is a foundational step in the process of welding where large sheets of metal are cut into specific shapes as needed.
There are many advanced techniques to make sure that metal cuts are clean and precise. For example, a plasma cutter uses electrically-conductive gas to send an extremely precise jet of hot plasma through the metal, resulting in extremely precise and fast cuts.
In some cases, cutting is the only step required for a metal fabrication project. However, typically it is simply the first step in a much larger process.
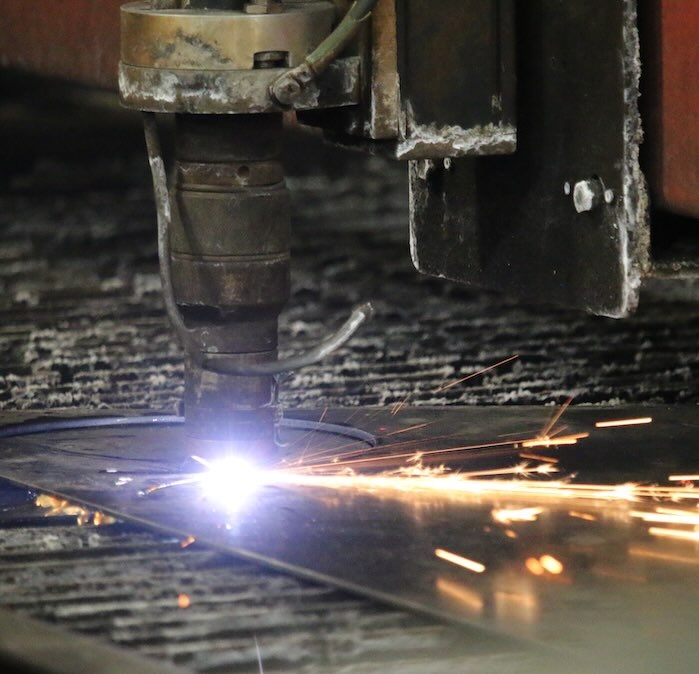
Welding
Welding is the process of joining metals together by melting and fusing them. Various methods like MIG welding (Metal Inert Gas, a courser method used for welding together thicker metals), TIG welding (Tungsten Inert Gas, a finer method typically used for welding together thinner metals), and arc welding utilize heat to create a strong bond between metal pieces.
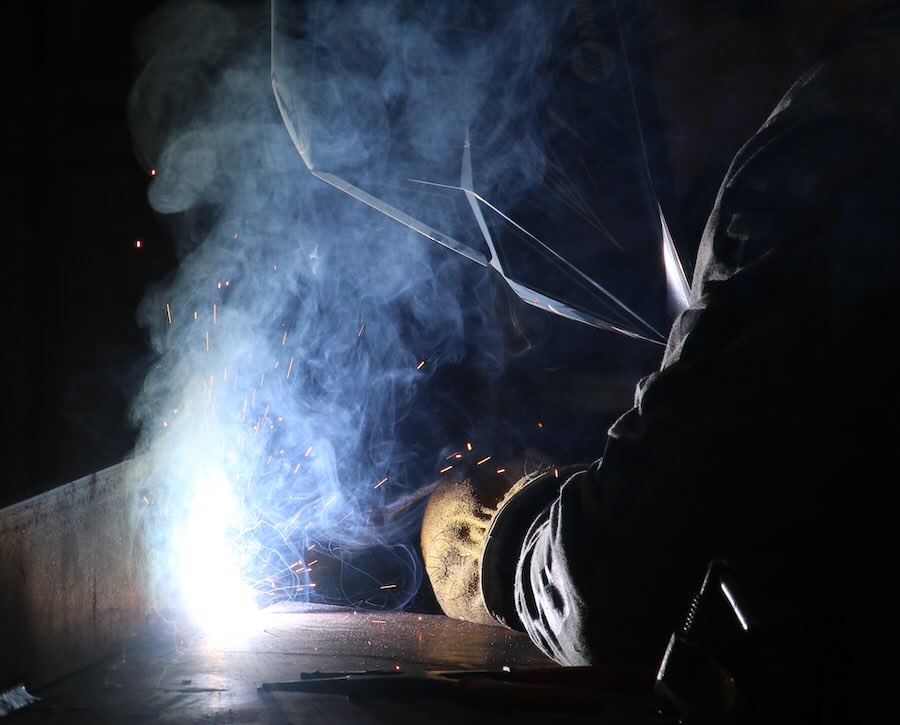
Machining
Machining involves the shaping of metal by cutting down a larger piece into a desired shape. Whereas cutting, which uses sheets of metal and a cutter, machining involves processes like milling, turning, drilling, and grinding use cutting tools which shape metals to precise specifications.
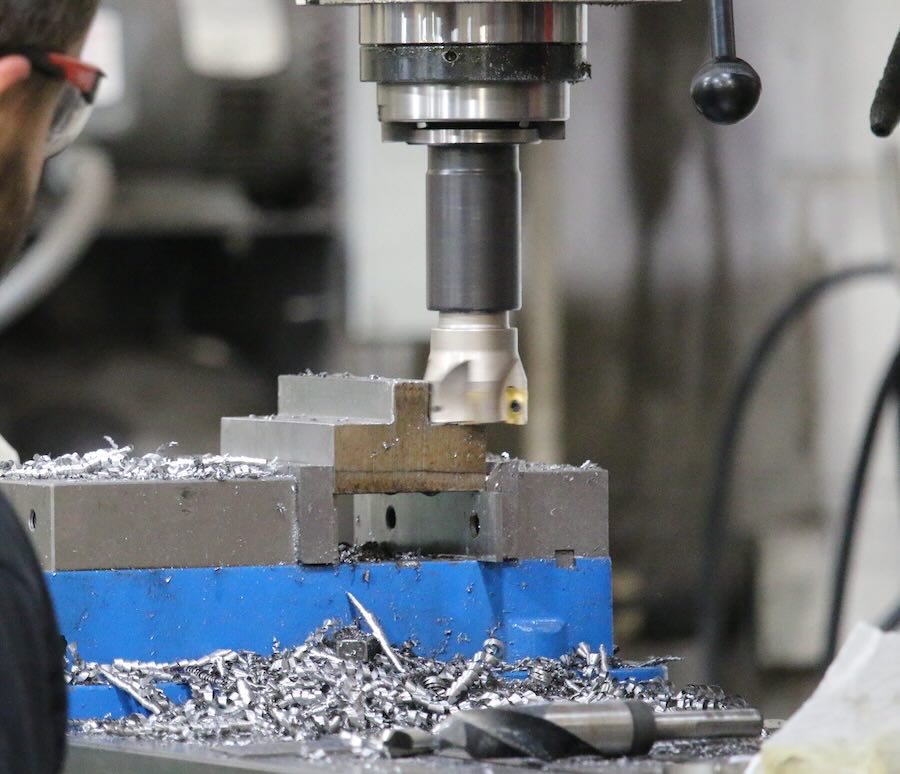
Assembly
An integral part of the fabrication process, assembly brings together fabricated components to create the final product. This stage encompasses various techniques, including riveting, bolting, and adhesion methods, where meticulous attention ensures the seamless integration of fabricated elements into a cohesive whole.
Beyond cutting, welding, machining, and assembly, metal fabrication embraces an array of specialized methods to meet specific project demands. Each technique in metal fabrication bears its unique significance, offering versatility and precision to cater to a broad spectrum of project requirements.
Commonly-Used Metals and Their Unique Applications
Metal fabrication involves a nuanced understanding of various metals, each selected for its distinct properties catering to specific applications. Let's delve deeper into some commonly used metals in fabrication:
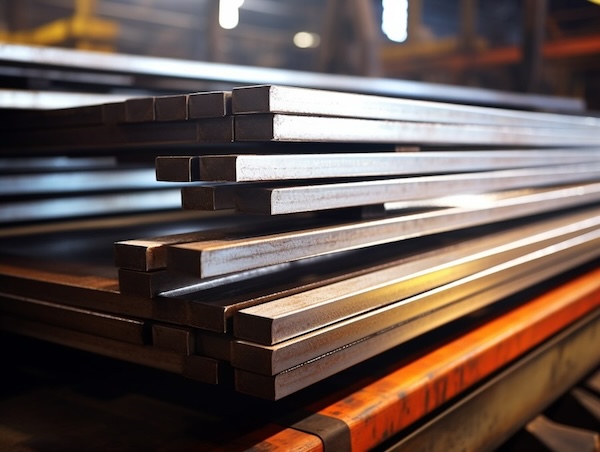
Steel
It's the workhorse of metal fabrication due to its exceptional strength and durability. Steel comes in different types, offering various strengths and hardness. It's extensively used in construction, machinery, automotive parts, and more.
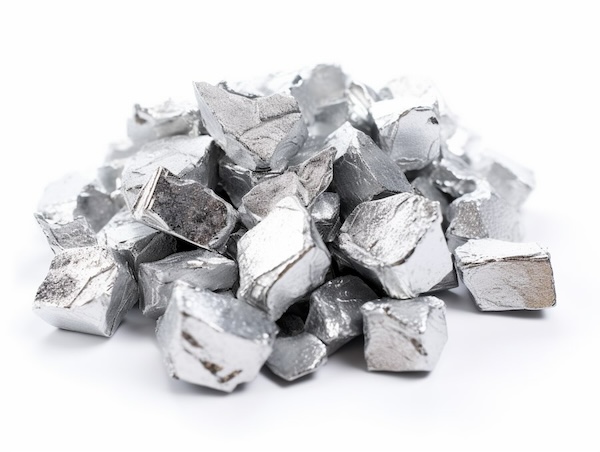
Aluminum
Known for being lightweight yet strong, aluminum is a go-to metal in industries where weight is a concern, like aerospace and automotive. Its corrosion resistance makes it ideal for outdoor applications as well.
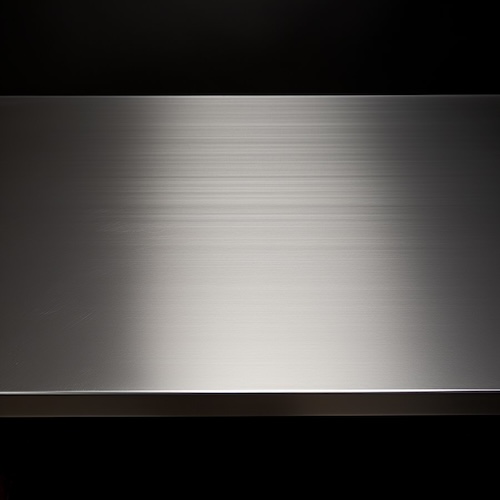
Stainless Steel
This metal is a favorite for environments where corrosion is a major concern. It's highly resistant to rust and corrosion, making it perfect for items used in harsh conditions, such as kitchen appliances, medical instruments, and architectural structures.
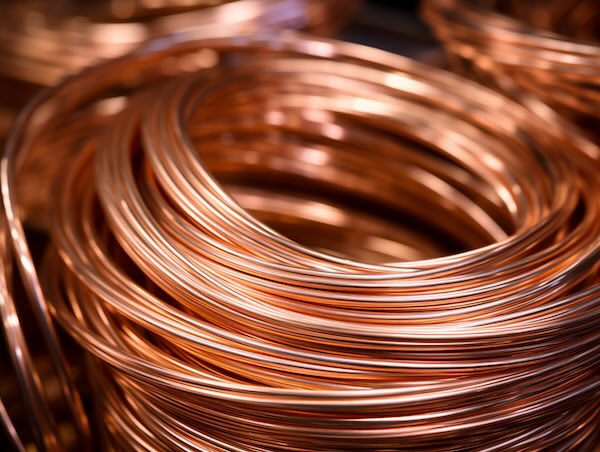
Copper
Famous for its excellent electrical conductivity, copper is indispensable in the electrical and electronics industry. It's used in wiring, electrical components, and in various electronic devices due to its ability to efficiently conduct electricity.
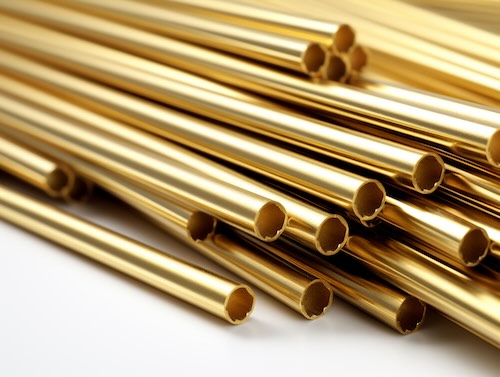
Brass
A blend of copper and zinc, brass is admired for its beautiful appearance and resistance to corrosion. It's commonly used in decorative items, musical instruments, plumbing fixtures, and fittings where both aesthetics and durability are important.
These metals provide a spectrum of properties that allow fabricators to choose the best material for each job. Whether it's about strength, conductivity, corrosion resistance, or aesthetics, selecting the right metal ensures that the fabricated product meets the specific requirements and performs optimally in its intended environment.
Quality Assurance
Metal fabrication intercepts with pivotal markets which demand both productivity and unwavering reliability. Therefore, it is of utmost importance that metal fabrication companies guarantee excellence in every manufactured product. At Shupe Fabrication, we diligently undertake meticulous measures to uphold high standards in our projects. Each product undergoes rigorous testing to ensure they uphold our reputation for high quality. Projects involving electronics are always signed off by a certified electrician. In the rare instance of dissatisfaction, our commitment remains resolute in rectifying any concerns to achieve complete satisfaction. Trust Shupe Fabrication for uncompromising quality and reliability in metal fabrication solutions.
Metal Fabrication—Highly Specialized, Yet Essential
In essence, metal fabrication embodies the intricate process of transforming raw metal into tailored components, utilizing a range of specialized techniques and materials. From the foundational stages of cutting, welding, machining, and assembly to the nuanced selection of metals like steel, aluminum, stainless steel, copper, and brass, this comprehensive overview delves into the multifaceted world of metal fabrication. It underscores the pivotal role of precision, expertise, and innovation in nurturing concepts into tangible, high-quality metal products. As highlighted by Shupe Fabrication's commitment to stringent quality assurance, this article encapsulates the essence of metal fabrication, showcasing its diverse applications, methodologies, and the inherent craftsmanship that shapes the modern world.
What is Shupe Fabrication?
Based in Idaho, Shupe Fabrication offers full-service, comprehensive, on-site hydraulic diagnosis and repair, as well as metal fabrication, for the northwest United States, including Idaho, Oregon, Washington, Utah, Montana, Wyoming, and Nevada. We provide a premium service with a guarantee.